One, scorch
1, the phenomenon of scorching
(1) The temperature reflects ultra-high, or the temperature of the control of the instrument fails, causing the plastic ultra-high temperature and scorch.
(2) The rubber exit of the nose has large smoke, strong irritating odors, and buzz.
(3) Particulate scorch appears on the plastic surface.
Wire and Cable
(4) There is a continuous air hole at the glue joint.
2, the cause of scorching
(1) Ultra-high temperature control causes plastic scorch.
(2) The screw is used for a long time without cleaning, and the burned material accumulates and is extruded with the plastic.
(3) The heating time is too long. The long-term heating of the plastic accumulation will cause the plastic to deteriorate and scorch.
(4) The parking time is too long, there is no cleaning head and screw, causing the plastic to decompose scorch.
(5) Change the mold or change color several times, causing the plastic to decompose scorch.
(6) The head gland is not compacted, and the plastic decomposes during aging.
(7) The instrument that controls the temperature malfunctions, resulting in scorching after the ultra-high temperature.
3, eliminate the method of scorching
(1) Check if the heating system is normal.
(2) Clean the screw or machine head regularly and thoroughly clean it.
(3) According to the requirements of the heating process, the heating time should not be too long. If there is a problem with the heating system, it should be promptly found by relevant personnel.
(4) Change the mold or color change promptly and cleanly to prevent variegated color or plastic scorching.
(5) After adjusting the mold, the mold cover should be pressed tightly to prevent the glue from entering.
(6) Found scorch should immediately clean the head and screw.
Second, poor plasticization
1, the phenomenon of poor plasticization
(1) There is a fur-like phenomenon on the surface of the plastic layer.
(2) The temperature control is low, the meter pointer reflects the low temperature, and the actual measurement temperature is also low.
(3) The surface of the plastic is black, and there are tiny cracks or small particles that are not plasticized.
(4) The plastic joints are not well stitched and there is a clear mark.
Wire and Cable
2. Causes of poor plasticization
(1) The temperature control is too low or the control is inappropriate.
(2) Hard plasticized resin particles in plastic.
(3) The operation method is not proper, the screw and pulling speed are too fast, and the plastic is not fully plasticized.
(4) The mixing of plastics during granulation is not uniform or the plastic itself has quality problems.
3, exclude the method of poor plastication
(1) Control the temperature according to the process regulations, and find that the temperature is low to properly increase the temperature.
(2) The speed of the screw and the traction should be appropriately reduced to increase the time for heating and plasticizing the plastic so as to increase the plasticizing effect of the plastic.
(3) The use of screw cooling water enhances the plasticization and tightness of the plastic.
(4) When selecting the mold, the mold sleeve is appropriately small to strengthen the pressure of the rubber mouth.
三、
1, the phenomenon of defects
(1) The crucible produced during the plasticization process of the resin has small crystal spots and small particles on the surface of the plastic layer and is distributed around the surface of the plastic layer.
(2) The crucible produced by scorching has a burnt substance on the surface of the plastic layer, which is particularly reflected on the surface of the glue joint.
(3) impurities, there are impurities on the plastic surface, there are impurities in the sliced crucible.
(4) Plastic crucibles resulting from poor plasticization. After slicing, it was found that the crucible was cooked.
2, the cause of defects
(1) Since the temperature control is low, the plastic has not been plasticized and is extruded from the nose.
(2) The plastics are of poor quality and are difficult to plasticize. These are not fully plasticized and are squeezed out.
(3) Some impurities are added to the hopper when charging, causing impurities.
(4) Ultra-high temperature control causes scorching, resulting in scorching.
(5) The molded lid is not compacted, aged and deteriorated after entering the gel, and scorching occurs.
3, the method to eliminate defects
(1) The defects caused by the plastic itself should be raised appropriately.
(2) Check the plastics strictly for impurities during feeding. Do not add other debris to the hopper when adding materials. Clean up the nose immediately after the impurities are found, and run the plastic inside the screw.
(3) It is found that if the temperature is excessively high, the temperature should be reduced appropriately. If the effect is not good, the head and the screw must be cleaned immediately to eliminate the scorch.
(4) Resin crucibles and poorly plasticized crucibles should be used, and the temperature must be increased or the speed of the screw and pulling should be reduced.
Fourth, the positive and negative plastic layer
1, the phenomenon of excessive production
(1) The speed of the screw and traction is unstable, and the current meter or voltmeter oscillates sideways, thus affecting the outer diameter of the cable and causing a deviation of the plastic layer.
(2) There is a problem with the quality of semi-finished products, such as loose wrapping of steel tape or plastic tape, uneven unevenness or defects in plastic layers such as wraps, edges, and pits.
(3) The ultra-high temperature control results in a reduction in the amount of extrusion, a sudden decrease in the outer diameter of the cable, and a thinning of the plastic layer to form a negative difference.
2, the cause of the poor
(1) The core or cable core is not round, but also has a serpentine shape, and the outer diameter changes too much.
(2) Semi-manufactured products have quality problems, such as: bad steel joints, loose steel belts, curling of steel belts, loose plastic tapes, excessive joints, scattered flowers, etc.
(3) When the operation is performed, the matching of the cores is too large, which may result in inverted plastics and plastic cores.
(4) When the mold is adjusted, the mold-adjusting screws are not tightened, resulting in a reversed buckle phenomenon that deviates the plastic layer.
(5) The screw or traction speed is unstable, causing an overshoot.
(6) The feeding port or the filter is partly blocked, resulting in a decrease in the amount of glue and a negative difference.
3, the method to exclude the poor
(1) Regularly measure the outer diameter of the cable and check the thickness of the plastic layer, and find that the outer diameter changes or the plastic layer is not uniform and should be adjusted immediately.
(2) The matching mold should be suitable. After adjusting the mold, tighten the mold adjusting screw and press the cover tightly.
(3) Pay attention to the current and voltmeter of the screw and traction and find it unstable.
(4) Do not add the material or other debris into the hopper. If this condition is found, remove it immediately.
Fifth, the cable diameter uneven and bamboo shape
1, the phenomenon of uneven thickness and bamboo shape
(1) The uneven diameter of the outer diameter of the cable due to unstable screw or traction.
(2) As the traction suddenly becomes unstable, the plastic forming the cable is bamboo-shaped.
(3) The mold matching is small, and the outer diameter of the semi-finished product changes greatly, resulting in uneven thickness of the plastic layer of the cable.
2. Causes of uneven thickness and bamboo shape
(1) The speed of the retractable line or traction is not uniform.
(2) The outer diameter of the semi-finished product varies greatly, and the mold is not properly selected.
(3) The screw speed is unstable, the main motor rotates unevenly, and the belt is too loose or slipping.
3, the method to exclude uneven thickness and bamboo shape
(1) Check the speed of the screw, traction, and take-up and release line regularly.
(2) The matching of molds should be suitable to prevent the phenomenon of inverted glue.
(3) Regularly check the operation of machinery and electrical appliances, find problems and immediately find fitters and electricians to repair.
Six, poor glue joints
1, bad glue joint phenomenon
(1) On the outside of the surface of the plastic layer, the plastic is not well-merged, there is a trace of hair and severe cracks.
(2) The plastic layer of the plastic layer is not well plasticized, and there are tiny particles that smash, and when it is severe, it is torn open by hand.
(3) The controlled temperature is low, especially the control temperature of the head is low.
2. Reasons for bad glue joints
(1) Low control temperature and poor plasticization.
(2) The head is used for a long time, causing serious wear and tear.
(3) The temperature control of the head failed, resulting in low temperature, making the plastic lamination glue not good.
3, eliminate the bad method of glue seam
(1) Appropriately increase the control temperature, especially the control temperature of the head.
(2) The outside of the nose is insulated by heat preservation devices.
(3) Add two layers of filters to increase the pressure and increase the degree of plasticization of the plastic.
(4) Properly reduce the speed of helicoidal traction and prolong the plastic plastification time to achieve the purpose of plastic splicing.
(5) Lengthen the wire diameter of the die to increase the extrusion pressure and temperature.
Seven other defects
1, air holes, air bubbles or air
(a) Cause
(1) Local control of temperature is extremely high.
(2) The plastic is damp or has moisture.
(3) The excess gas in the plastic after parking is not excluded.
(4) Wet natural environment.
(b) Remedy
(1) The temperature control should be appropriate, and the temperature should be adjusted immediately to prevent excessive local temperature.
(2) Check the plastic quality strictly when adding materials, especially during the rainy season. If there is water in the plastic, it should be stopped immediately, and then run off the moisture.
(3) Add a preheating device at the feeding place to drive off the moisture and moisture in the plastic.
(4) Always sample and inspect the plastic layer for air holes, air bubbles, and air bubbles.
2, disjointed or broken plastic
(I) Reasons for the origin
(1) Conductive cores have water or oil
(2) The core is too heavy to make local contact with the core, causing the temperature to decrease, causing local cooling of the plastic, resulting in disjoint or broken plastic due to stretching of the plastic.
(3) The quality of the semi-finished products is poor, such as the loosening of the steel tape and the plastic tape, and the joint is not strong or large.
(b) Remedy
(1) Mould selection should be larger, especially the matching jacket mould, to enlarge 6 to 8mm.
(2) Properly reduce the length and thickness of the core nozzle.
(3) Reduce the speed of the screw and traction.
(4) Adjust the control temperature of the head appropriately.
3, pits and eyes
(a) Cause
(1) The tightly pressed conductive core is not tightly stranded and has voids.
(2) The core has water, oil, and dirt.
(3) Defective semi-finished products, such as stranding, pressure drop, crossover, bending, overlap of strips and plastic tapes, loose sleeves, large joints, etc.
(4) Lower temperature control.
(b) Remedy
(1) The tight pressure of the stranded conductor must comply with the process regulations.
(2) Semi-finished products do not meet quality requirements and should be processed before production.
(3) Remove dirt, core or core to warm up.
4, plastic layer from the bag, edges, ears, folds and bumps
(I) Cause
(1) Quality problems caused by plastic wrapping and steel belt wrapping.
(2) The size of the mold is too large and it is caused by vacuum.
(3) After the core is damaged, plastic is poured.
(4) The outer diameter of the core is too large, and the plastic layer does not cool well.
(b) Remedy
(1) Check the quality of semi-finished products, non-conforming products do not produce.
(2) Change the unsuitable mold
(3) Replace the mold.
(4) Increase the flow rate of cooling water and reduce wire production speed.
Henan Sanheng Industrial Co., Ltd. , founded in 2000, It is one of the top wire and cable manufacturers in China's wire and cable industry for nearly 20 years. the company has more than 5 production lines.
The production cable can be divided into more than 50 varieties and subdivided into 1000 specifications.All products have passed national certification, such as China compulsory certification, bv certification, Nigerian SONCAP certificate, China national industrial certification, etc. China national industrial production license, etc.It also has the ability to produce products that meet international standards, such as iec, ce, rohs, etc.
If you want to buy wires and cables, you can ask the customer service staff and we will get back to you as soon as possible.
-
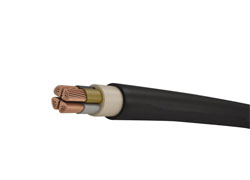
600-1000V CU XLPE Power Cable
Conductor:Bare Copper Conductor of Class 1/2 (Solid)
Insulation:XLPE Compound
Insulation Color:Red, Blue, Grey, Yellow/Green or as request
-
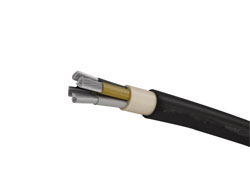
600-1000V AL XLPE Power Cable
3500 V:Bare Aluminum Conductor of Class 1/2 (Solid)
Insulation:XLPE Compound
Insulation Color:Red, Blue, Grey, Yellow/Green or as request
-
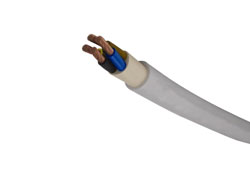
600-1000V Flexible Power Cable
Conductor:Bare Copper Conductor of Class 5 (Flexible)
Insulation:PVC Compound
Insulation Color:Red, Blue, Grey, Yellow/Green or as request
-
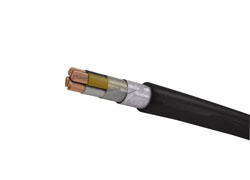
600-1000V SWA Armoured Cable
Conductor:Bare Copper Conductor of Class 1/2 (Solid)
Insulation:XLPE Compound
Insulation Color:Red, Blue, Grey, Yellow/Green or as request