Section 6 Laying of Cables on Bridges
Article 5.6.1 The cable on the wooden bridge shall be laid with pipes. Cables laid on bridges of other structures shall be provided with cable trenches under the sidewalk or in pipelines made of refractory material. In places where people do not easily contact, cables can be laid bare on the bridge, but measures should be taken to avoid direct sunlight.
Article 5.6.2 The net distance between the cable and bridge structure erected shall not be less than 0.5m.
Article 5.6.3 The cables laid on bridges that are often subjected to vibration shall have anti-vibration measures. Cables at both ends of the piers and expansion joints should have slack.
Chapter 6 Fabrication of Cable Terminals and Connectors
Section 1 General Regulations and Preparations
Article 6.1.1 The production of cable terminations and connectors shall be carried out by trained personnel familiar with the process.
Article 6.1.2 The production of cable terminations and joints shall strictly comply with the production process regulations; the oil-filled cables shall also comply with the relevant regulations of the oil and vacuum processes.
Article 6.1.3 When making outdoor 6kV and above cable terminals and connectors, the air relative humidity should be 70% or less; when the humidity is high, the ambient temperature or heating cable can be increased. 110kV and above high-voltage cable terminal and joint construction, temporary sheds should be used, the ambient humidity should be strictly controlled, the temperature should be 10 ~ 30 °C. When making plastic insulated power cable terminals and connectors, dust and debris should be prevented from falling into the insulation. Construction in fog or rain is strictly forbidden.
Fire-fighting equipment shall be available at the indoor and oil-filled cable construction sites. Temporary power supply should be provided for the construction in the room or tunnel.
Article 6.1.4 35kV and below cable terminations and connectors shall meet the following requirements:
First, the type, specifications should be consistent with the cable type such as voltage, number of cores, cross-section, sheath structure and environmental requirements.
Second, the structure should be simple, compact and easy to install.
Third, the materials used, parts should meet the technical requirements.
Fourth, the main performance shall comply with the provisions of the current national standard "Basic Performance Requirements for Power Cable Accessories with Rated Voltage of 26/35kV and Below".
The additional insulating material used in Clause 6.1.5 shall be compatible with the insulation of the cable body except that the electrical performance shall meet the requirements. The physical properties of the two materials, such as hardness, expansion coefficient, tensile strength, and elongation at break, should be similar. Rubber and plastic insulated cables should be made of materials with large elasticity and good adhesive properties as additional insulation.
Article 6.1.6 of the cable core connection fittings, should be used in accordance with the standard connection pipe and terminals, its internal diameter should be closely matched with the cable core, the gap should not be too large; section should be 1.2 ~ 1.5 times the core cross section. When crimping is used, the crimping pliers and the die should meet the specifications.
Article 6.1.7 Control cables may have joints under the following conditions, but they must be firmly connected and should not be subjected to mechanical tension.
First, when the length of laying exceeds the length of its manufacture.
Second, it is necessary to extend the already installed control cables.
Third, when eliminating the cable failure in use.
Article 6.1.8 Before making cable terminations and connectors, you should be familiar with the installation process data, make inspections, and meet the following requirements:
First, the cable insulation is in good condition without moisture; the plastic cable must not be filled with water; before the oil-filled cable is constructed, the cable body, pressure box, cable oil drum and paper roll drum should be taken one by one to make electrical performance tests, and should meet the standards. .
Second, the specifications of the accessories should be consistent with the cable; parts should be complete without damage; insulation material must not be exposed to moisture; sealing materials must not fail. The shell structure accessories should be pre-assembled to clean the inner wall; the test seals, and the structural dimensions meet the requirements.
Third, the construction equipment is complete, easy to operate, clean conditions, complete material consumption, clean the plastic insulation surface of the solvent should follow the process guidelines prepared.
Fourth, if necessary, test assembly should be carried out.
Article 6.1.9 of the power cable grounding wire should be copper stranded or tinned copper braided wire, and its cross-sectional area should not be less than the provisions of Table 6.1.9. The cross-sectional area of 110 kV and above cables should meet the design requirements.
Table 6.1.9 Cable terminal grounding section
Cable cross section (mm2) Ground wire cross section (mm2)
120 and below 16
150 and above 25
Article 6.1.10 The connection of cable terminals and electrical devices shall comply with the relevant provisions of the current national standard "Code for the Construction and Acceptance of Busbar Installations of Electrical Installation Engineering".
Section II production requirements
Article 6.2.1 Preparation of cable terminations and connectors shall be performed continuously from the time of stripping the cable until completion, shortening the insulation exposure time. Stripping the cable should not damage the core and the remaining insulation. Additional insulation wrapping, assembly, heat shrink, etc. should be cleaned.
Article 6.2.2 When the oil-filled cable line has a joint, a joint should be made first; when there is a position difference at both ends, the low-level terminal head should be made first.
Article 6.2.3 Cable terminations and joints shall be reinforced by measures such as reinforced insulation, sealed moisture, and mechanical protection. Terminals and connectors for power cables of 6 kV and above shall have effective measures to improve the electric field concentration at the end of the cable shield and shall ensure the distance between the external insulation and the ground.
Article 6.2.4 of the 35kV and below cable in the stripping cut core insulation, shielding, metal sheath, the minimum distance of the core along the insulating surface to the nearest ground point (shield or metal sheath end) should meet the requirements of Table 6.2.4 Claim. Table 6.2.4 Minimum distances in cable terminations and connections Rated voltage (KV) Minimum distance (mm) 150 6100 10125 35250
Article 6.2.5 Plastic Insulated Cables When making terminal heads and connectors, the semi-conductive shield should be completely removed. For the coated graphite shield, solvent should be used to wipe off the carbon traces; for the extruded shield, the insulating surface must not be damaged when stripped, and the shield end should be flat.
The 6.2.6 three-core oil-paper insulated cable shall retain the insulation of the package 25mm, and shall not be damaged. Strip the masking carbon ink paper and the end should be flat. When the core is bent, the force should be evenly applied, and the insulation paper should not be damaged; the bending radius of the core should not be less than 10 times its diameter. When wrapping or pouring, filling insulation material, the air gap at the branch of the core should be eliminated.
Article 6.2.7 When the oil-filled cable terminals and joints are wrapped around additional insulation, the pressure tanks must not be completely closed. When making neutralization and vacuum treatment, the oil that leaked from the cable should be discharged in time, and should not accumulate in the porcelain sleeve or casing.
Article 6.2.8 When the cable core is connected, the oil and oxide layers on the inner wall of the core and connecting pipe shall be removed. Crimping molds and fittings should fit properly. The compression ratio should meet the requirements. After crimping, the tabs on the terminal or connecting pipe should be repaired and smoothed so that no burrs remain. Use solder to connect the copper core, should use neutral solder paste, not burn insulation.
The metal shielding layer (or metal sheath) and armor layer of the cable on both sides of the 6.2.9 section three-core power cable connector shall be connected well and shall not be interrupted. The cross-section of the cross-section shall not be less than the section 6.1.8 of the grounding wire in this specification. Provisions. The metal sheath of the cable connector and the metal sheath of the cable shall be treated with anti-corrosion treatment.
The metal sheath at the end of the 6.2.10 three-core power cable must be well grounded; the copper shield and the steel sheath of the plastic cable should be soldered to the ground. When the cable passes through the zero-sequence current transformer, the metal sheathing of the cable and the grounding wire should be insulated. When the cable grounding point is below the transformer, the grounding wire should be grounded directly; when the grounding point is above the transformer, the grounding wire should pass through the transformer. Grounding.
Article 6.2.11 When assembling and assembling cable terminations and joints, plugging, moisture proofing, and sealing measures must be taken at the fittings or overlaps between the various components. Lead-coated cable should be wiped off the surface oxide when it is sealed; lead and lead should not be too long, and the seal must be dense and non-porous. The lead seal of the oil-filled cable shall be carried out in two parts. The first time the oil is plugged, the second one is formed and reinforced, and the high-position lead seal is reinforced with epoxy resin.
Plastic cables should be sealed with self-adhesive tapes, adhesive tapes, and adhesives (hot-melt adhesives). The surface of the plastic sheath should be roughened. The surface of the plastic sheath should be treated with a solvent to remove oil and the adhesion should be good.
Cable terminals, connectors, and oil-filled cable supply lines should not leak.
The installation of the oil supply system for oil-filled cables in accordance with 6.2.12 shall meet the following requirements:
1. There should be insulation joints between the metal tubing and the cable termination of the oil supply system, and its insulation strength should not be lower than the outer sheath of the cable.
Second, when multiple pressure tanks are installed in each phase, they should be connected in parallel.
Third, each phase of the cable line should be equipped with hydraulic monitoring or alarm devices.
Fourth, the instrument should be installed firmly, outdoor instruments should have rain measures, after the completion of construction should be set.
Fifth, adjust the pressure of the pressure tank, so that it should not exceed the allowable pressure range of the cable under any circumstances.
The 6.2.13 cable terminal should have a clear phase mark, and should be consistent with the phase of the system.
Article 6.2.14 The control cable terminal can be used for general dressing, and the joint should be protected against moisture.
Henan Sanheng Industrial Co., Ltd. , founded in 2000, It is one of the top wire and cable manufacturers in China's wire and cable industry for nearly 20 years. the company has more than 5 production lines.
The production cable can be divided into more than 50 varieties and subdivided into 1000 specifications.All products have passed national certification, such as China compulsory certification, bv certification, Nigerian SONCAP certificate, China national industrial certification, etc. China national industrial production license, etc.It also has the ability to produce products that meet international standards, such as iec, ce, rohs, etc.
If you want to buy wires and cables, you can ask the customer service staff and we will get back to you as soon as possible.
-

PVC Insulated Aluminum Cable
Conductor:Aluminum Conductor of Class 1/2 (Solid)
Insulation:PVC Compound
Insulation Color:Red, Blue, Green, Yellow, Brown, Black, Grey, White, Pink, Orange, Yellow/Green
-
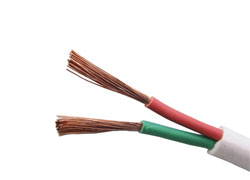
Flexible Flat Cable
Conductor:Stranded Copper Conductor of Class 5/6 (Flexible)
Insulation:PVC Compound
Insulation Color:Red, Blue, Yellow/Green or as request
-
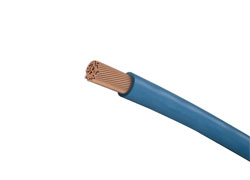
Single Core Flexible Cable
Conductor:Stranded Copper Conductor of Class 5 (Flexible)
Insulation:PVC Compound
Conductor Color:Red, Blue, Green, Yellow, Brown, Black, Grey, White, Pink, Orange, Yellow/Green
-
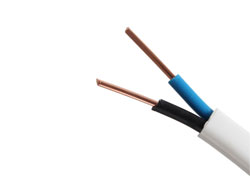
Twin and Earth Cable
Conductor:Class 1/2 copper conductor (solid)
Insulation:PVC Compound
Insulation Color:Red, Blue, Yellow/Green or as request